Missing teeth can do more than just affect a smile—they can impact confidence and daily comfort. Dental implants in Como offer a modern solution for those looking to restore both function and appearance with natural-looking results. More people are choosing this proven treatment to regain their bite and boost self-esteem.
From the first consultation to the final result patients in Como are discovering how dental implants can transform their oral health. With advanced techniques and personalised care it’s never been easier to enjoy a complete smile again.
What Are Dental Implants?
Dental implants replace missing teeth using small titanium posts placed in the jawbone. Implants provide a secure base for fixed or removable replacement teeth, such as crowns, bridges, or dentures. Patients gain improved comfort, strong chewing ability, and appearance that matches natural teeth.
Clinicians at JC Dental Como use digital scanning and 3D imaging during the consultation to assess bone density and plan accurate implant placement. They recommend dental implants for patients in Como seeking solutions for single or multiple missing teeth, provided there’s adequate jawbone and good oral health.
Implants fuse with the bone over several months, creating a stable foundation. This process, called osseointegration, reduces the risk of slipping, unlike removable dentures. Dental implant crowns resemble real teeth in shape and colour, restoring both confidence and function.
Dentists at JC Dental Como monitor healing and tissue health throughout the procedure to optimise long-term outcomes. They explain post-treatment care to minimise discomfort and ensure implant success. Dental implants offer a permanent solution for restoring missing teeth, with survival rates above 95% after five years according to Australian Dental Association data.
Key Benefits Of Dental Implants Como
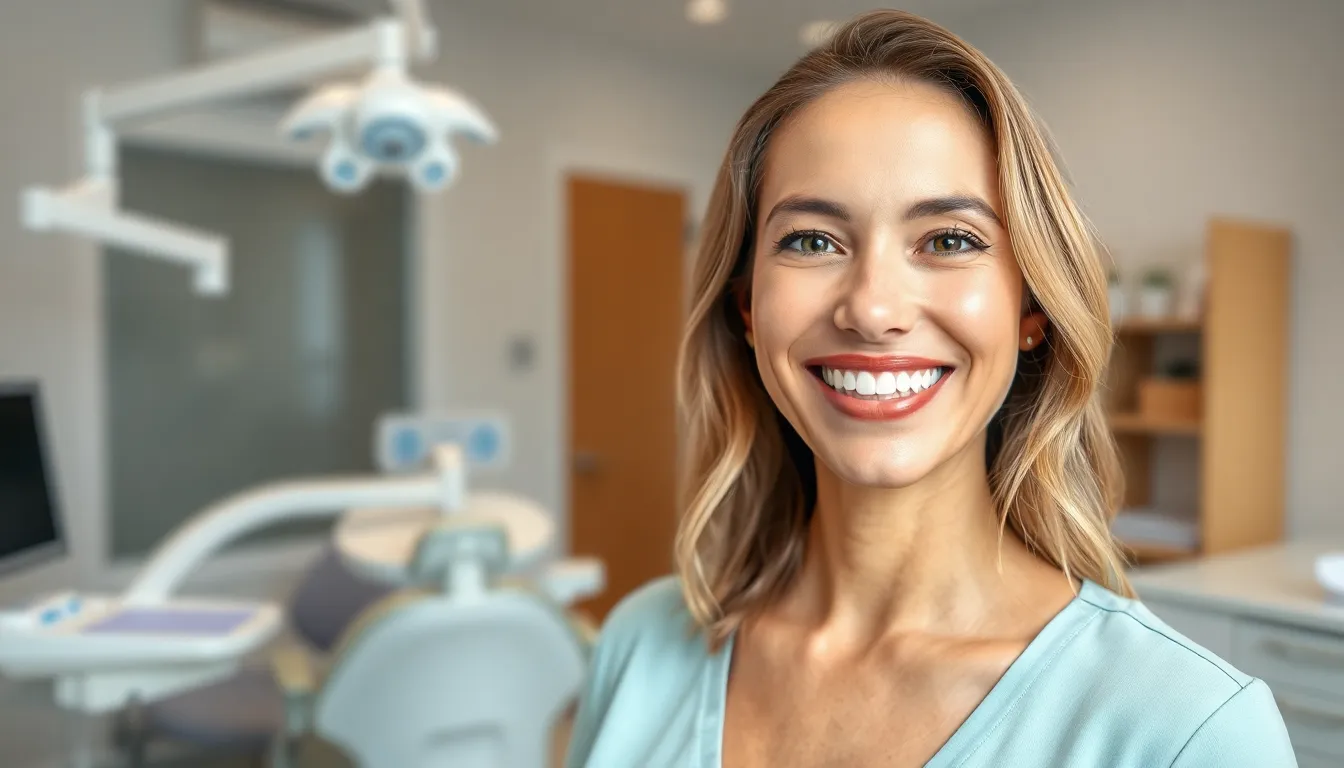
Dental implants in Como deliver functional and aesthetic benefits for patients missing teeth. Implants provide a durable solution, with a success rate above 97% over 10 years according to international studies. Titanium posts used in each dental implant resist wear and corrosion, often lasting for decades with routine oral care provided at clinics like JC Dental Como.
Implants closely match healthy, natural teeth, supporting a lifelike appearance and comfort unavailable with most dentures or removable bridges. Many patients report stable speech and improved chewing strength compared to traditional tooth replacement options. JC Dental Como customises dental implants using digital scanning, helping ensure crown alignment and bite accuracy for each case.
Fixed implants strengthen jawbone integrity. Tooth loss often leads to up to 30% alveolar ridge bone reduction soon after extraction; dental implants help maintain bone volume by stimulating bone tissue, supporting facial contours and oral health long-term.
Self-esteem gains follow improved speech clarity and an attractive, gap-free smile. Patients at JC Dental Como often mention renewed confidence in work and social situations after implant treatment.
JC Dental Como’s multidisciplinary approach means patients gain access to family-focused care, post-surgical monitoring, and a full suite of cosmetic and preventive dental services—delivering stability, comfort, and long-lasting results with every dental implant.
The Dental Implant Procedure In Como
Dental implant procedures in Como involve careful planning, advanced diagnostics, and meticulous restoration, all with a focus on patient comfort and optimal results. JC Dental Como provides a comprehensive approach using digital technology and skilled practitioners to ensure each step meets local clinical standards.
Consultation And Planning
Consultations at JC Dental Como start with detailed assessments using a clinical examination, digital X-rays, and 3D CBCT scans to confirm bone density and structure. Dentists identify implant suitability for every patient, considering oral health, gum condition, and any missing teeth. Treatment plans outline options, including need for preparatory procedures like bone grafting or sinus lifts, which replace lost bone for better implant stability. Dentists discuss costs, anaesthesia choices, and expected timelines with each patient. Full-mouth scans allow for precise mapping of implant positions and prediction of aesthetic results, which helps clinicians replicate natural smiles and functions. Patients receive details on aftercare protocols, expected surgery outcomes, and the overall procedure’s steps.
Surgical Placement And Recovery
Dentists at JC Dental Como perform implant placement under local anaesthetic, with IV sedation available for anxious patients. A small incision in the gum exposes the jawbone, then dental surgeons drill a targeted hole to fit a titanium post. Sutures close the site, beginning the healing phase. Most implants are left undisturbed for 3–6 months to permit osseointegration, which permanently fuses the post to the jawbone for stability. Some clinics offer same-day temporary teeth, but most patients wait for full recovery before fitting the final crown. Recovery visits track bone integration, and post-operative protocols reduce the risk of infection and discomfort. Detailed follow-ups ensure that healing progresses well and patients get tailored advice for oral hygiene. Once integration is confirmed, dentists proceed to the final restoration phase, completing the tooth replacement for seamless chewing, speech, and appearance.
Choosing The Right Clinic For Dental Implants In Como
Selecting a dental implant clinic in Como relies on expertise, technology, and patient-focused service. When researching potential dental providers, patients often consult resources like the Best Dental Clinics in Como Directory to compare available options and read detailed practice information.
Experienced implantologists such as Dr. Tiziano Testori and the DENS clinical team have performed substantial numbers of implant procedures, achieving high success rates and consistent results. Clinics in Como that use advanced diagnostic tools, for instance 3D imaging and digital scanners, gain precise bone density measurements before planning surgery, supporting safety and accuracy in implant placement.
Personalised treatment plans determine the suitability of dental implants for each patient, with assessments covering jawbone quality, oral health, and gum condition. Clinics like DENS and Dr. Testori‘s provide tailored consultations, addressing individual concerns and recommending specific implant systems.
Patient comfort remains central to leading clinics. Options for sedation or anxiety management, available at Dr. Testori‘s clinic, help ease the treatment process, supporting those with dental anxiety. Comprehensive services, including full arch restorations, gum therapy, orthodontics, and bone regeneration, deliver integrated solutions for patients with complex dental needs.
Patients in Como seeking confident, predictable outcomes can focus on clinics with track records in diagnostics, surgical precision, and aftercare. For those considering treatment options, consulting Exceptional Dental Care Como: Top Practice Recommendations provides valuable insights into leading practices and their specialised services.
In Western Australia, JC Dental Como applies these same standards, combining digital technology, experienced practitioners, and a full spectrum of restorative and cosmetic dental options to optimise long-term results for implant patients. The practice has been recognised in various professional directories, including the JC Dental Featured Among Top 10 Como Dentists in WA ranking, highlighting their commitment to excellence in implant dentistry.
Why JC Dental Como Stands Out
JC Dental Como has established itself as a leading provider of dental implant services in the Perth metro area. The practice’s reputation for excellence is reflected in their inclusion in the Top-Rated Dentist Directory Featuring JC Dental Perth, where patients can access detailed information about their services and credentials.
The clinic’s comprehensive approach to dental implant treatment combines state-of-the-art technology with personalised patient care. Their team of experienced dental professionals uses advanced diagnostic equipment, including 3D CBCT imaging and digital treatment planning, to ensure optimal outcomes for every patient. This commitment to excellence is showcased in their JC Dental Como Professional Practice Overview, which details their full range of implant services and patient-centered approach.
JC Dental Como’s multidisciplinary team ensures that patients receive comprehensive care throughout their implant journey. From initial consultation through final restoration, the practice maintains strict quality standards and follows evidence-based protocols to achieve consistently successful outcomes.
Cost And Financing Options For Dental Implants
Dental implant costs in Como reflect standard Italian pricing. Single dental implants typically range from €850 to €1,500 per implant, with an average cost of €1,082.5 depending on the clinic and technical complexity. More extensive treatments, such as full-mouth implants or All-on-8 solutions, cost between €8,500 and €12,000 per arch, averaging €10,133. Clinics near Milan, including those in Como, follow similar cost structures based on practitioner reputation and procedure scope.
Payment solutions in Italian clinics aim to make dental implants more accessible. Patients access payment plans, international patient packages, or partial coverage through dental insurance if the treatment is medically indicated. Payment plans often allow instalments over several months, some with interest-free periods. Personal loans, health savings accounts (HSAs), or flexible spending accounts (FSAs) provide additional alternatives for managing larger out-of-pocket costs.
In Australia, JC Dental Como offers competitive pricing tailored to comprehensive patient assessment. Flexible payment options include staged payments and finance plans with minimal or no interest after approval. The clinic supports private health cover rebates, which may contribute toward implant costs when meeting eligibility guidelines. Expert staff guide patients through the cost breakdown, pre-approval for health fund rebates, and tailored quotation during consultation, ensuring clarity and transparency at every stage.
Treatment Type | Typical Cost Range (€) | Average Cost (€) |
---|---|---|
Single Dental Implant | 850–1,500 | 1,082.5 |
All-on-8 / Full-Mouth (per arch) | 8,500–12,000 | 10,133 |
Conclusion
Choosing dental implants in Como opens the door to a renewed sense of confidence and lasting oral health. With advanced technology and skilled clinicians on hand patients can expect a seamless experience from consultation to final results.
Personalised care and modern techniques ensure that every step is tailored for comfort and success. Those considering dental implants will find that Como’s clinics offer not just expertise but also flexible payment options to make treatment accessible.
A complete smile is within reach for anyone ready to take the next step towards improved function and appearance.
Frequently Asked Questions
What are dental implants?
Dental implants are small titanium posts placed in the jawbone to act as artificial tooth roots. They provide a secure foundation for crowns, bridges, or dentures, offering a stable and natural-looking replacement for missing teeth.
How do dental implants improve comfort and confidence?
Dental implants restore full chewing ability and look like real teeth, helping you eat, speak, and smile confidently. Patients often report feeling more comfortable and self-assured in social and professional situations.
What is the success rate of dental implants in Como?
According to the Australian Dental Association, dental implants have a survival rate over 95% after five years. Clinics in Como, such as JC Dental, report success rates even higher, particularly with proper care and maintenance.
Who is a good candidate for dental implants?
Ideal candidates have healthy gums, adequate jawbone density, and good oral hygiene. Advanced diagnostics, such as 3D scans, help determine your suitability for dental implant treatment.
What is involved in the dental implant procedure?
The procedure includes an initial consultation, digital assessments, and personalised treatment planning. Implants are surgically placed under local anaesthetic, followed by a healing period and fitting of the final restoration once osseointegration is complete.
How long do dental implants last?
With proper oral care, dental implants can last for decades. Most high-quality implants in Como offer durability, resisting wear and corrosion, with success rates above 97% over ten years.
Are dental implants better than traditional dentures?
Yes, implants offer superior stability, comfort, and chewing strength. They help prevent jawbone loss and do not slip like removable dentures, providing a look and feel close to natural teeth.
How much do dental implants cost in Como?
Single dental implants typically cost between €850 and €1,500, averaging €1,082.5. Full-mouth solutions can range from €8,500 to €12,000 per arch. Many clinics offer payment plans and finance options.
Is the dental implant process painful?
Most patients experience minimal discomfort. Implants are placed under local anaesthetic, with sedation available for anxious patients. Any post-surgery discomfort is usually mild and managed with pain relief.
Why choose JC Dental Como for dental implants?
JC Dental Como combines expert implantologists, advanced digital technology, and patient-centred care. They offer flexible payment options, thorough aftercare, and consistently high success rates for lasting results.